
10 K&C Tests You Need for Your CarSim Model
Building an Accurate CarSim Model
CarSim, a vehicle simulation software produced by Mechanical Simulation, is a powerful and complex tool. When building an accurate model in CarSim it is important to use real-world test data. This data is crucial in both building and verifying the model. Without the use of physical test data, it is easy to fall into the garbage-in-garbage-out trap.
You should include many types of physical test data in a CarSim model, but suspension kinematics and compliance (K&C) data is about as foundational as it gets. CarSim allows you to import vehicle properties into a model via expanded Parsfiles through a simple process. In just a few clicks, a properly built file can import massive amounts of physical test data.
Here at Morse Measurements, we have been running K&C tests and building Parsfiles for CarSim models for years. We’ve determined the tests to run to build an accurate model. This combination of kinematic and compliance tests not only provides the necessary data for CarSim but also reveals much about the suspension system. We break these required tests down into two categories: kinematic tests and compliance tests.
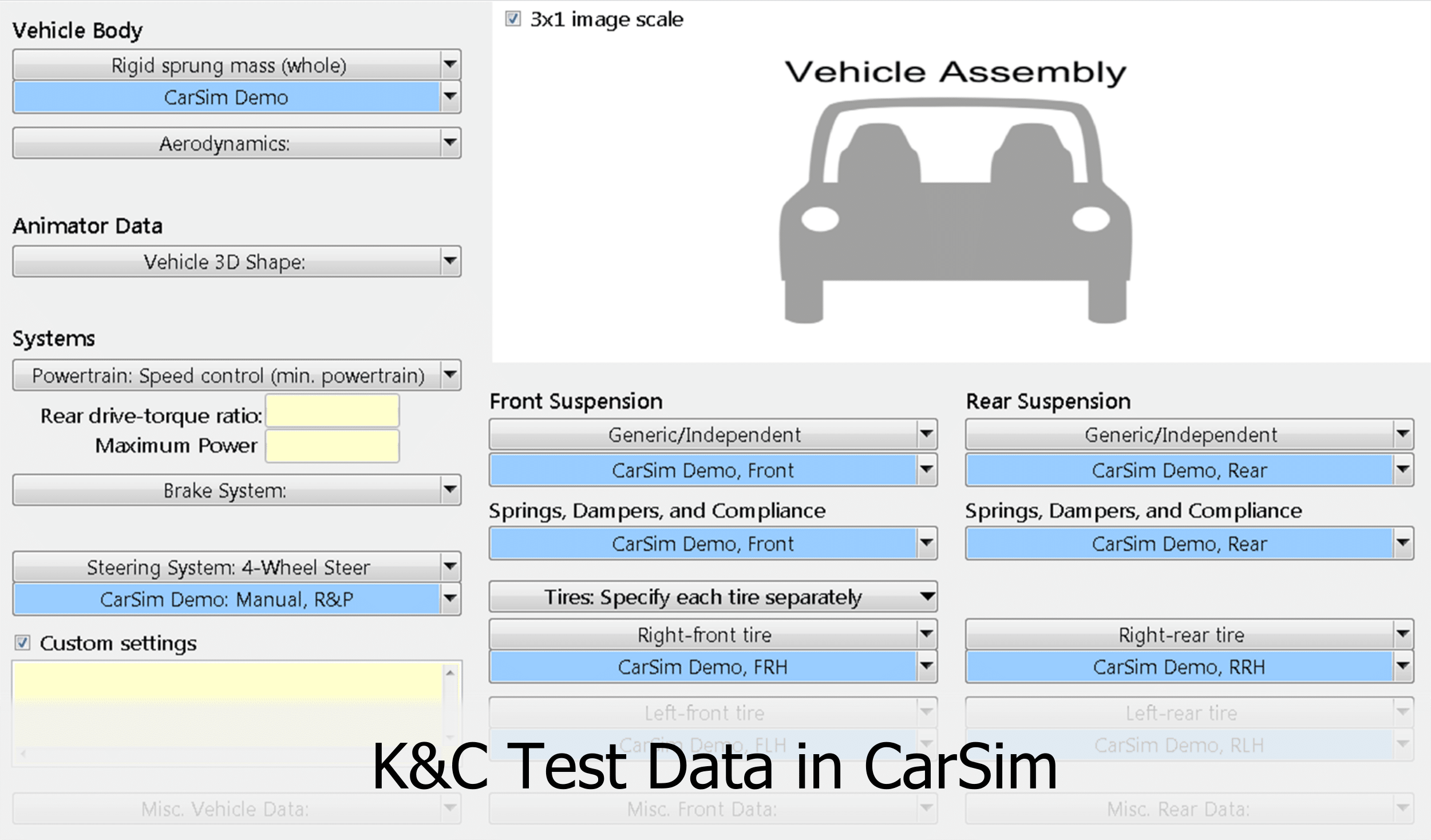
Kinematic Tests
We use kinematic tests to understand the geometry of the suspension; the geometry is defined by the various suspension links and their connections. Kinematics are an essential component of the CarSim model. The kinematic tests required to build out a CarSim model are the bounce test, the bounce-pitch test, two roll tests (with and without anti-roll bars attached), and a steering test.
During each kinematic test, the rig maintains forces and moments at zero at each tire contact patch, thus canceling any unwanted tire “scrub” forces, and allowing the suspension to move freely.
Each Kinematic test (and each Compliance test) runs at a snail’s pace. These long cycle times (around 1 minute) remove the unwanted damper and inertial forces from the tire vertical load measurements. The K&C rig measures loads, displacements, and wheel orientations at each of the four wheels throughout every test.
Bounce and Bounce-Pitch Test
The bounce test is the most basic kinematic test, but it doesn’t lack importance. In a bounce test, the rig moves the vehicle chassis in pure bounce motion within defined bounds. The bounce-pitch test adds vehicle pitch to capture the behavior of the suspension across its full travel. Using bounce AND pitch motion, the K&C rig can account for differences in travel between the front and rear.
We import a whole host of parameters from the bounce and bounce-pitch tests into the CarSim Parsfile. Wheel camber, toe, lateral, and longitudinal movements with respect to vertical load are all imported. These parameters are essential to modeling a vehicle suspension system. We also import spring properties and tire deflection into the CarSim Parsfile from the bounce and bounce-pitch tests.
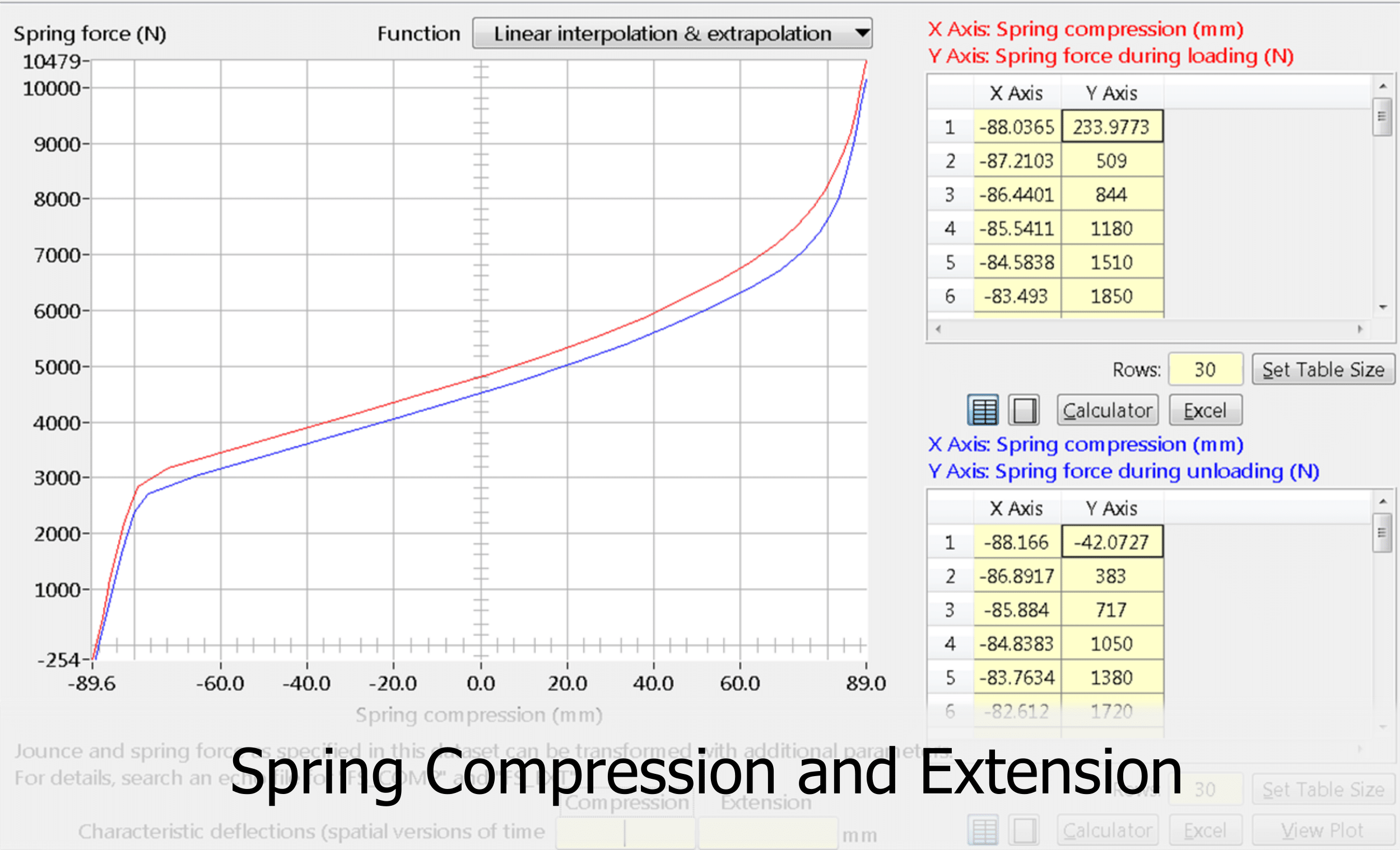
Roll Tests
Two fixed axis roll tests further build out the CarSim model. A fixed axis roll test rolls the vehicle about a fixed axis in the ground plane by actuating the center table in roll. For the CarSim model, we run two different fixed axis roll tests. First, we run a test with the anti-roll bars attached like normal. We then detach the anti-roll bars and run the test again. Through this process, we isolate the effect of the anti-roll bars on the suspension.
Running both tests allows us to calculate the auxiliary roll moment for the CarSim model. We first calculate the suspension roll moment at each axle with and without the anti-roll bars. The difference between the moments at each axle is the auxiliary roll moment required by the CarSim model. The auxiliary roll moment is one of the many datasets we import from the roll tests.
Steering Test
A steering test holds the chassis fixed while sweeping the steering wheel through its range of displacement, lock-to-lock. This is done with the Anthony Best Dynamics steering robot. During the test, the K&C rig maintains zero scrub force at the tire contacts and measures forces and wheel orientations at each of the steered wheels.
One parameter revealed by the steering test that we include in the CarSim Parsfile is the road wheel steer. This real-world data provides a vital piece of a complete and accurate CarSim model.
Compliance Tests
Kinematic tests provide the backbone of a suspension model. They show the basic behavior and characteristics that you must get right. Compliance tests fill out the model with the result of real-world flexing, bending, and shifting. In compliance tests, we apply real-world forces and/or moments to the vehicle wheels. The result is a better understanding of how compliant the system is…and where that compliance is. We use lateral, longitudinal, and aligning torque tests to build a CarSim Parsfile.
In CarSim, there are two ways to define compliance properties. You can define the compliance with a simple linear rate or with nonlinear tables. Using a linear rate has distinct disadvantages. With most compliance characteristics, a linear rate will only be able to accurately describe a small segment of the total range. Widening the range covered by the linear rate will average in more of the total curve, but oftentimes creates a rate that is not representative of most of the vehicle response. The second method is to import a non-linear lookup table that captures the full vehicle response. We employ this method by measuring and importing the full range of compliance characteristics.
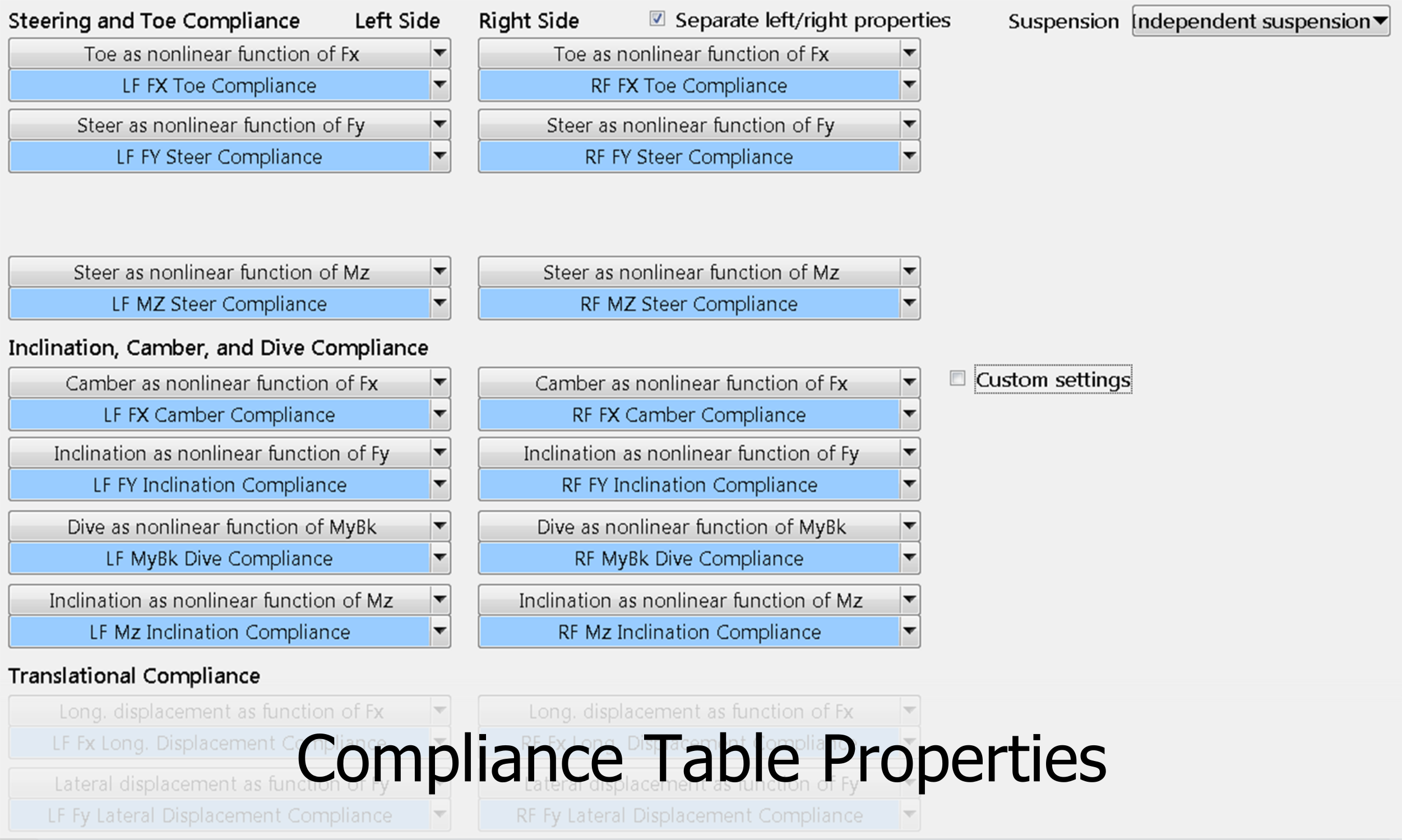
Lateral Compliance Tests
During a lateral compliance test, the rig holds the vehicle chassis fixed while applying lateral forces through each of the four tire contact patches. The lateral force acts in line with the center of tire contact pressure. We use two types of lateral compliance tests to build a CarSim model: lateral parallel (in-phase) and lateral opposed (out-of-phase). As the names imply, lateral forces are applied in the same direction at the same time in a parallel test and in opposite directions in an opposed test. We use both the lateral parallel test and lateral opposed test to build the CarSim Parsfile.
With these two tests, we measure several characteristics used by the CarSim model. The wheel inclination and wheel steer are both included in the file as a function of lateral force. In a solid axle vehicle, the axle lateral displacement is also included.
Aligning Torque Compliance Tests
In aligning torque compliance tests, the K&C rig drives ground plane torques into each of the four tire contact patches. As with the lateral compliance tests, we use parallel and opposed aligning torque tests. In a parallel aligning torque test torque acts through each wheel in the same direction (i.e. all torques clockwise, and/or all torques counter-clockwise); while in an opposed test, torques act in opposite directions.
We use data from these two tests to determine the wheel steer compliance as torque is applied. This is one dataset from the aligning torque tests that we include in the CarSim Parsfile.
Longitudinal Compliance Test
In a longitudinal compliance test, the rig holds the chassis fixed while applying longitudinal forces through the tire contact patches. We perform this test in many ways, but for the CarSim model, we use a braking longitudinal compliance test. In the braking test, we actuate the brakes and apply longitudinal forces in the braking direction to the tire contact patches.
This test reveals to us how the suspension reacts to real-world braking loads. We import parameters like the longitudinal displacement of the axle, camber change, and toe change into the Parsfile.
Putting it All Together
By running each of the above tests, we can construct an expanded Parsfile that you can use to easily create a model in CarSim. We combine these core tests with a few others so that you can validate your model with real-world data. In the end, you will have a more accurate model and—perhaps just as importantly—you will have the confidence that comes with knowing exactly how that model compares to the real car you’re modeling.
If you’d like to learn more about our simulation support (for CarSim, CarMaker, or ADAMS) check out this page; or contact us using the form below.
Call Now: 704.638.6515
Call Now:
704.638.6515
1163 Speedway Blvd.,
Salisbury, NC 28146
Phone: 704.638.6515
Fax: 704.638.6516
Info@MorseMeasurements.com
© 2025 Morse Measurements | Powered by Miller Davis
1163 Speedway Blvd., Salisbury, NC 28146
Phone: 704.638.6515
Fax: 704.638.6516
Info@MorseMeasurements.com
© 2025 Morse Measurements | Powered by Miller Davis